Pressure-sensitive adhesive, commonly referred to as PSA, is an adhesive that becomes tacky when pressed and stays sticky once released. This makes PSA the perfect solution for label or tape applications that require a secondary layer of support. Instead of being applied directly to a surface,
PSA is typically coated onto a backing material like paper or a piece of woven fabric, which is then cut into smaller pieces and packaged as tape or labels. When these secondary layers are applied to a product with primary labeling requirements such as barcodes or logos, the PSAs remain inactive until pressure is applied.
When pressure is released, the PSAs activate and remain sticky so they’re ready for another round of pressure or removal. Although there are many types of PSA available today, most can be categorized into one of three main groups: general-purpose PSAs (often referred to as gP), direct printable PSAs (dP), and hot melt prepackaged PSAs (hMP).
Each group has different attributes and uses specific to that type of PSA. Read on to learn more about them all!
Read More: What Are The 6 Most Common Types of Adhesives?
General Purpose (gP) PSAs
General-purpose PSAs are an example of a pressure-sensitive adhesive that is a good all-around adhesive with low tack, low viscosity, and good adhesion. These PSAs work well for a variety of applications and have a moderate adhesion strength and peel strength.
General-purpose PSAs can be used for many different label applications, such as labeling bottles, boxes and jars for food products, clothing, industrial products and more. These are often used on porous and non-porous surfaces like paper, plastics, cardboard, fabric, and foil.
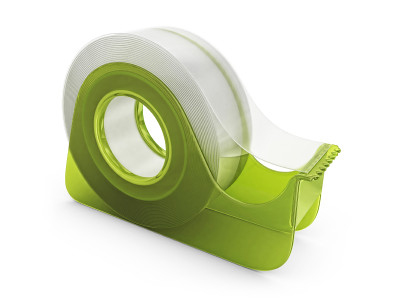
Image Source: Flickr
Direct Printable (dP) PSAs
Direct printable PSAs are also an example of a pressure-sensitive adhesive with low tack, low viscosity, and good adhesion. Direct printable PSAs are designed to be printed directly onto a surface without the use of a release liner since the adhesive on the back of the label is applied directly to the surface.
Direct printable PSAs can be used for a wide range of labeling applications, including apparel and textiles, home and garden, children’s toys and books, food, and industrial labeling. These PSAs are often used on non-porous surfaces like paper, cardboard, some types of fabrics, plastics, and foil.
Hot Melt Prepackaged (hMP) PSAs
Hot melt prepackaged PSAs are another example of a pressure-sensitive adhesive that has a low tack, low viscosity, and good adhesion. Hot melt prepackaged PSAs are pre-applied to a paper or woven fabric backing and then cut into smaller pieces that are packaged as tape or labels.
This type of PSA is often used for industrial labeling and packaging applications, such as labeling pallets or cartons, or packaging items like electronics or pharmaceutical products. These PSAs are often used on porous and non-porous surfaces like cardboard, paper, and fabrics.
Tips for Choosing the Right PSA
When it comes to selecting the right PSA for your applications, it’s best to start with the basics and consider the desired end-use applications, the label design, and the surface type of the product.
Read More: How to Apply Pressure Sensitive Adhesive?
What is an example of a pressure-sensitive adhesive?
An example of a pressure-sensitive adhesive exhibits tack upon initial contact and then exhibits shear flow properties when the force is removed.
What is the pressure-sensitive adhesive used for?
Pressure-sensitive adhesive is used to bond one or more materials together without the use of heat or underlying surface preparation. PSAs are commonly used in label and tape applications, where they are applied as a secondary layer that is then applied over a primary label or logo.
When applied correctly, PSAs create a bond between the backing surface and the product’s surface so that the label or tape stays in place even if the product is moved or handled roughly.
Because PSAs are applied as a secondary surface, they’re removable and are a great option for companies with frequent labeling and packaging requirements.
PSAs can also be used for bundling applications, like securing cables or wires together, and for packaging applications, such as the creation of clamshell packaging for food products.
Last Opinion
The best advice for selecting the right PSA for an application is to consider the product’s surface type and the intended usage of the product. Once those factors are known, it’s easy to determine which group of PSAs would be the best option for the application.
Once you’ve narrowed down the options, you can start testing different PSAs to see which one best meets your needs and expectations. With the right PSA, you can create strong bonds between materials of all types and get the long-lasting adhesion you need.